Efficiency enhancements in the shaft center
Manufacturing at DEUTZ is now even cleaner and more efficient thanks to extensive automation
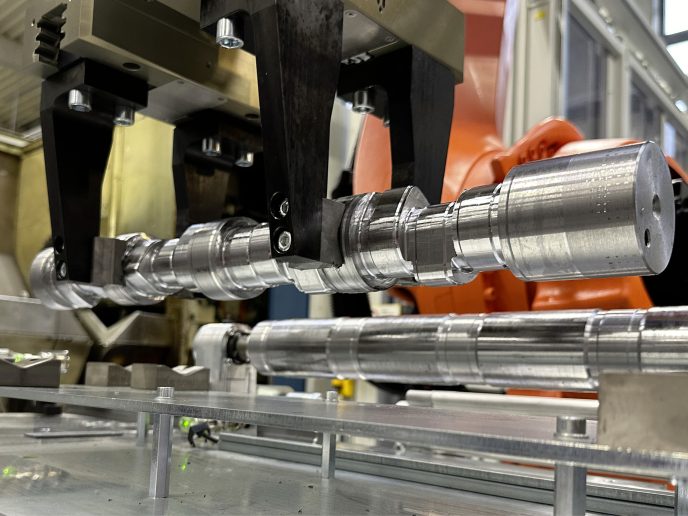
Crankshafts and camshafts for DEUTZ engines are manufactured at the 13,500m² shaft center in Cologne-Porz. The center has three production lines for each component, enabling us to produce up to 165,000 crankshafts and up to 230,000 camshafts for various engine series each year. A maximum of 16 different processing steps are needed to produce each shaft, carried out by a total of 120 machines.
When the plans for the shaft center were drawn up in 2014, lean principles aimed at optimizing the value chain were taken into consideration. The production-line-based design, which reduces the distances that items need to be moved, has already made production much more efficient and transparent. Since 2020, we have also increasingly been focusing on automation in order to boost productivity and make employees’ jobs less physically demanding.
Three new automated processes with robot loading went into operation in our shaft center in 2023. Implementing new automation technology takes around ten months and involves many different steps, starting with an analysis of commercial viability. The processes and software solutions are then modified, the occupational health and safety concept is drawn up and implemented, and employees undergo training. “In one of our production lines, we linked three machines from three different manufacturers thanks to automation, achieving a productivity gain of 20 percent,” reports Gerhard Fischer, who served as plant manager for the shaft center for many years until his retirement in February 2024.
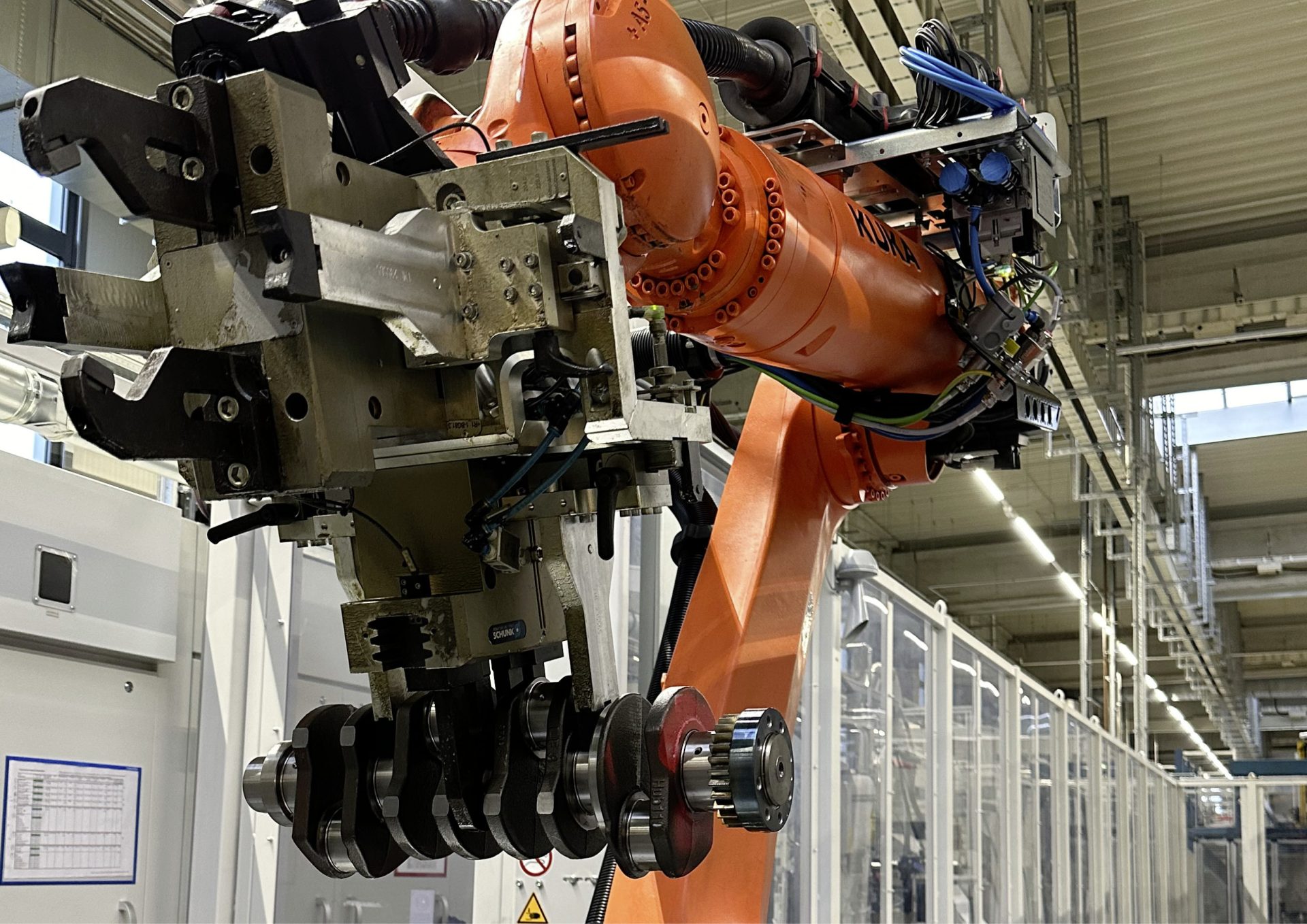
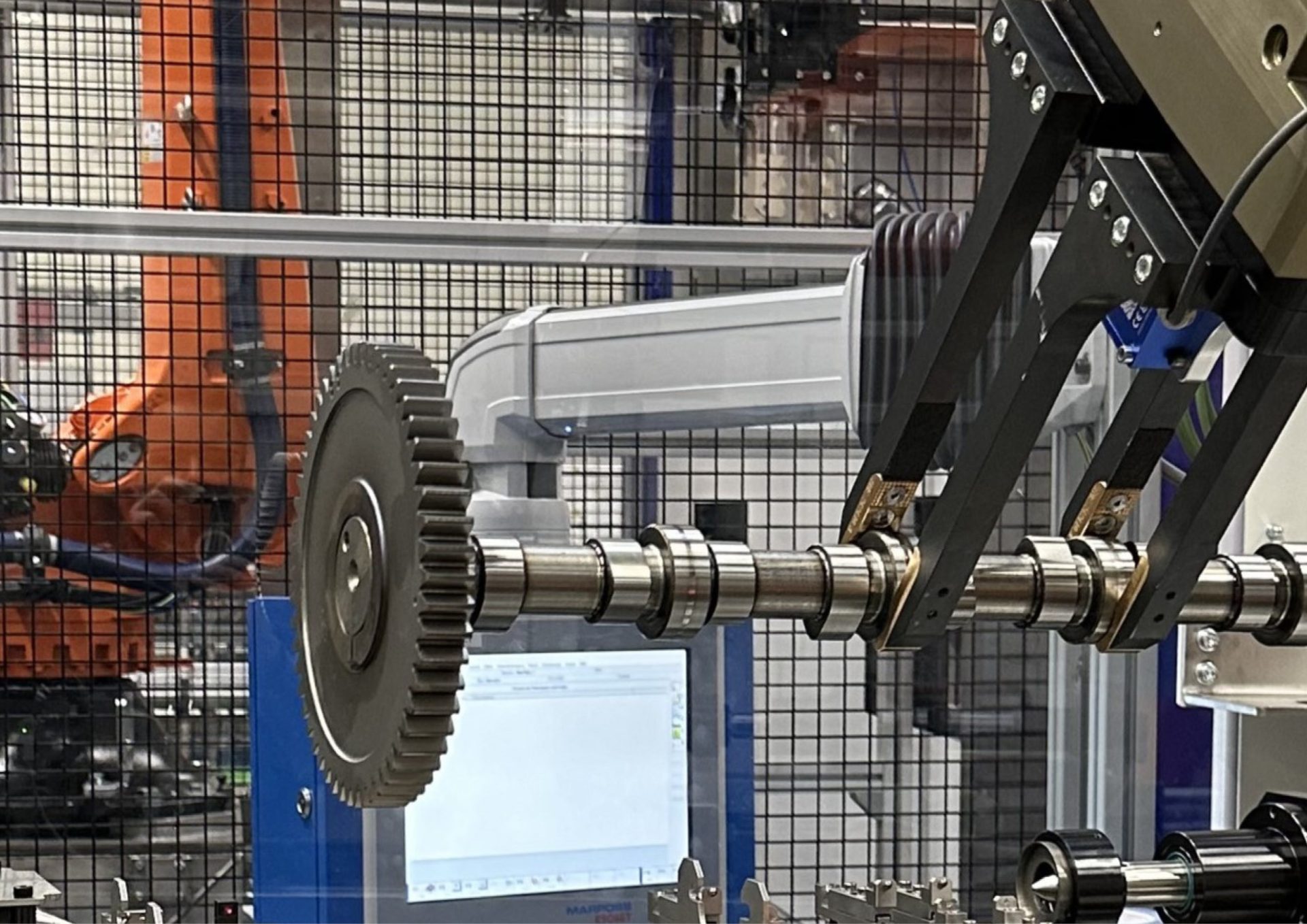
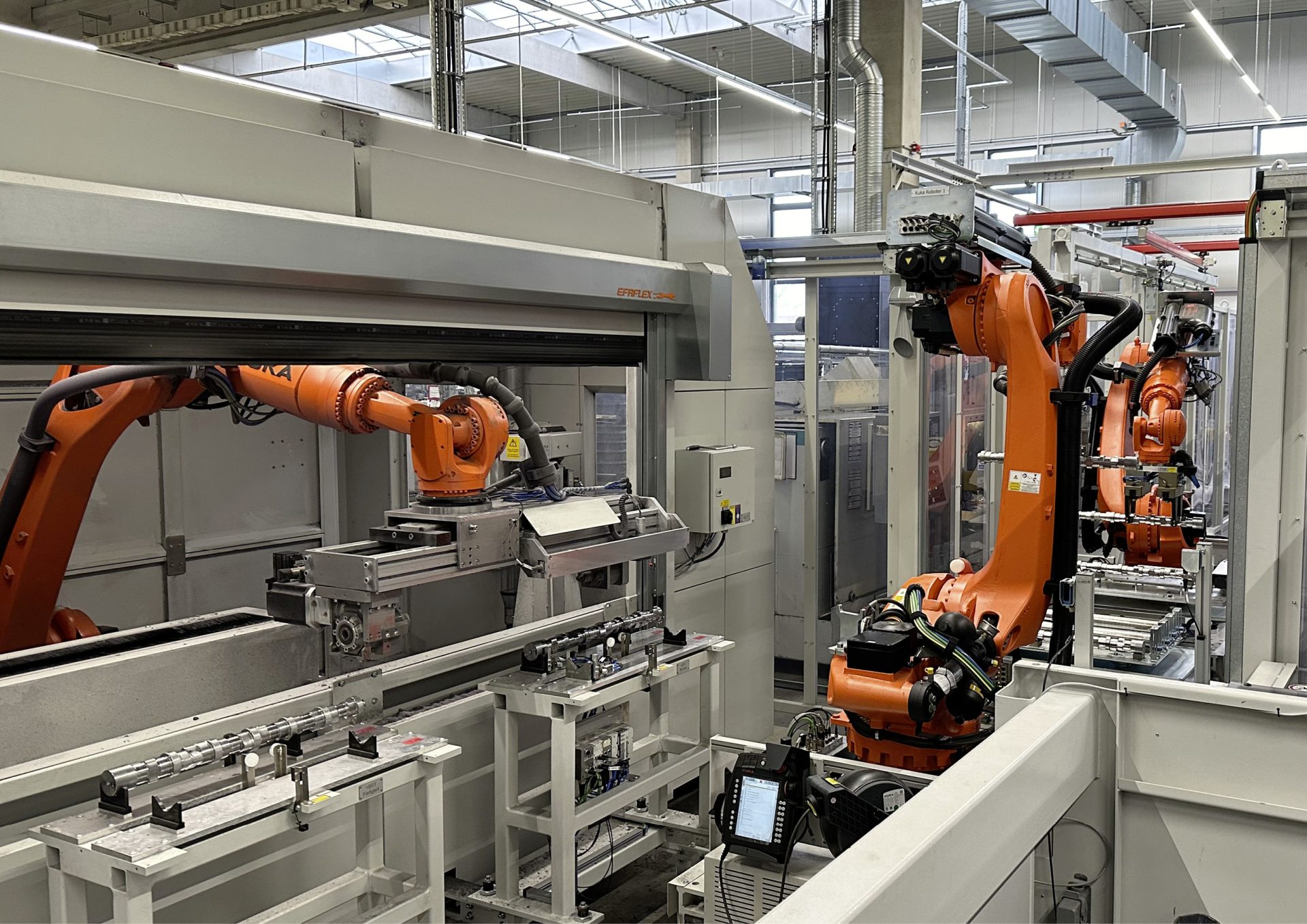
October 2023 saw the start of the first automation project for camshaft production, which is even more advanced. The entire pre-production process has now been automated in one production line, enabling different variants to be processed in parallel. Camera visualization is used to automatically remove the shafts from the transportation containers and put them back in again after processing.
In addition to efficiency, sustainability also plays a major role
in all automation projects. We are taking steps to improve our ecological footprint, such as by implementing a new cleaning system that uses solvent-free cleaning products without any loss of quality. This is much better for environment.
DEUTZ is refining shaft production on an ongoing basis. For example, digital process monitoring is helping us to further improve the first-time quality metric. Going forward, an AI-based notification system should help us to respond and intervene quickly in the event of process deviations. We are therefore well equipped for the years ahead.